In Zukunft: noch komplexer
C 52 | PW 3000 | C 42 | Präzisionsbearbeitung für Aerospace und Halbleiterindustrie
Wer additive Fertigung mit präziser Zerspanung verknüpft, liebt die Komplexität. toolcraft nutzt beide Technologien und überrascht am Ende seine Kunden mit zuvor unerreichter Qualität. Mitverantwortlich ist das durchdachte Maschinenkonzept von Hermle.
„Heute könnte noch was gehen auf dem Brombachsee“, deutet Jonas Billmeyer eines seiner Hobbys an: Windsurfen. Es ist Freitagmittag, die Sonne scheint, und das Wochenende ist nur noch wenige Stunden entfernt. Kein Grund für den Leiter des Bereichs Zerspanung bei toolcraft unruhig zu werden. Statt weiter über den nahegelegenen Surfspot im Süden Mittelfrankens zu reden, zeigt er, was ihn bei toolcraft antreibt. Es ist die Herausforderung, komplexe Aufgaben nicht kompliziert erscheinen zu lassen. Hinzu kommt ein Arbeitsumfeld, das zu eigenverantwortlichem Arbeiten und kreativen Pausen einlädt – mit Kicker und Badeteich. Firmengründer Bernd Krebs ist die familiäre Atmosphäre wichtig. Innerhalb von 30 Jahren entwickelte er zusammen mit den beiden weiteren Geschäftsführern Karlheinz Nüßlein und Christoph Hauck die toolcraft AG zu einem Unternehmen mit knapp 400 Kollegen – Krebs bevorzugt diese Bezeichnung –, das zukunftsweisende Technologien lebt.
Der Hauptsitz des mittelständischen Familienunternehmens ist in Georgensgmünd im mittelfränkischen Landkreis Roth – knapp zehn Kilometer vom Brombachsee entfernt. Mit seiner anthrazit abgesetzten Fassade, den Sichtbetonwänden und hohen Decken verspricht das Gebäude ein modernes Arbeitsklima. Die Produktion verteilt sich auf mehrere Hallen hinter dem Hauptgebäude. Die Nutzfläche beträgt insgesamt knapp 14.300 Quadratmeter. „toolcraft wächst organisch und hat noch Platz für mehr“, erzählt Jonas Billmeyer auf dem Weg durch seinen Verantwortungsbereich: Hallen voller 5-Achs-Fräszentren und Fräs-Drehautomaten, Dreh- und Flächenschleifmaschinen sowie Sägen. Allein 29 der Bearbeitungszentren kommen aus Gosheim, von der Maschinenfabrik Berthold Hermle AG.
-
Für mehr autonome Laufzeit kombinierte toolcraft einige der der High-Performance-Bearbeitungszentren von Hermle mit Palettenwechslern. -
Der PW 3000 hat auf zwei Ebenen Platz für acht Paletten. -
Sind die Schwenktüren geschlossen, ist der Weg frei für den Palettenwechsler. -
Die Einarbeitung auf der neuen C 52 U geht schnell – das Bedienkonzept des Hermle-Bearbeitungszentren ist identisch zu den kleineren Maschinen. -
Bereit für den nächsten Bearbeitungsschritt: Ein Werkstück für die Halbleiterindustrie in der C 52 U. -
Vom Pulver zum Triebwerk
Der Gang durch die Fertigung entspricht den Entstehungsprozessen mancher Werkstücke. Den Anfang machen 13 Metall-Laserschmelzanlagen. In dem Raum herrscht Überdruck, Abluftschläuche leiten die Staubdämpfe weg von den Maschinen. Funkend lassen Faserlaser komplexe Strukturen für die Luftfahrt, den Sondermaschinenbau, den Motorsport und die Halbleiterproduktion aus dem Metallpulver wachsen. toolcraft investierte schon früh in die additive Fertigungstechnik – mit Erfolg. Jonas Billmeyer nennt zwei entscheidende Vorteile: Die Funktionsintegration und die Verarbeitung hochfester Materialien. Er nimmt ein Bauteil aus einer Holzkiste. Die Aufschrift verrät, dass es sich um einen Auftrag aus der Luftfahrtbranche handelt. Die Oberfläche ist noch stumpf und rau. „Natürlich könnten wir sowas aus dem Vollen fräsen. Der Materialverbrauch und vor allem der Werkzeugverschleiß wären jedoch extrem hoch“, erklärt er. Vorsichtig legt er das Bauteil wieder zurück. Hier wartet es auf den Feinschliff unterm Fräser. Bohrungen, Gewinde und Passungen können nicht gedruckt werden.
Eine Tür weiter liegt der charakteristische Geruch von Kühlschmiermittel in der Luft. Hier beginnt die Zerspanung. Jonas Billmeyer erzählt, dass bereits 20 bis 25 Prozent der Zerspanungskapazität durch die Nachbearbeitung der additiv gefertigten Teile in Anspruch genommen werden – Tendenz steigend. Denn nahezu alle der aufgeschmolzenen Werkstücke werden nachbearbeitet. Darüber hinaus drehen, fräsen und schleifen er und seine Mitarbeiter für die Halbleiterindustrie und Luftfahrttechnik. Die restliche Kapazität fällt auf andere Branchen wie den Rennsport. Zielstrebig durchquert er Halle um Halle. Der Anblick ist ähnlich: Bearbeitungszentren mit und ohne Automation, Regale mit verschiedenen, zum Teil unfräsbar geformten Werkstücken. Es ist übersichtlich und aufgeräumt.
„Hermle gehört zu den besten Fräsmaschinen, die du kaufen kannst“, sagt Bernd Krebs anfangs. Der Maschinenpark bestätigt seine Überzeugung. Andere Hersteller sind dort vertreten, wo das Hermle-Konzept an seine Grenzen stößt und die Bauteildimensionen zu groß sind.
Billmeyer öffnet weitere Türen. Arbeitsbereiche mit kleinen und großen Anlagen, dazwischen der Kicker für die Pause. Nach einem kurzen Gang über den Innenhof erreicht er die Maschine, die für toolcraft ein Novum ist. „Normalerweise bearbeiten wir Bauteile ab einem Meter Länge auf Anlagen eines anderen Herstellers. Diesmal haben wir uns auch bei Hermle umgeschaut“, erzählt der Bereichsleiter. Die technischen Vorteile überzeugen. „Der Tisch ist komplett überfahrbar. Das Werkzeug erreicht in einer Operation jeden Punkt, ohne dass der Tisch rotieren muss. Damit erreichen wir die geforderten hochgenauen Ebenheiten in der Oberfläche.“
Präzision in groß
Die C 52 U mit dem Palettenwechsler PW 3000 steht ganz hinten. Durch die Drehtür des Rüstplatzmoduls sind zwei Regale sichtbar, mit Platz für sechs Paletten auf zwei Ebenen. Fahr-, Dreh- und Hubachsen bewegen den Wechsler mit der Palette zielsicher vom Regalplatz zum Maschinenarbeitsraum. Durch die Automationslösung von Hermle kann Zerspanungsmechanikerin Jasmin Zippel hauptzeitparallel rüsten. Theoretisch. Noch fährt sie die Maschine ein, die erst seit knapp zwei Monaten in Georgensgmünd zuhause ist. Auch wenn die Mechanikerin vorher noch nie an einer C 52 U stand, kommt sie problemlos zurecht. Das Bedienkonzept kennt sie schon von den kleineren Hermle-Anlagen bei toolcraft. Neu für sie ist die HACS-Software für den Palettenwechsler. Das „Hermle Automation Control System“ ist einer der fünf digitalen Bausteine des Maschinenbauers für eine smartere Produktion. Die Software berechnet Laufzeit und Werkzeugeinsatz, gibt einen Überblick über Arbeits- und Ablaufpläne, Paletten und Aufgaben, die Zippel erledigen muss. Per Drag-and-Drop dirigiert sie die Paletten und bestätigt Hermles Versprechen: Die Bedienung der HACS-Software ist durchweg intuitiv.
Auch wenn die Automation noch nicht voll eingebunden ist, fräst die C 52 U bereits erste Teile für die Halbleiterbranche: Zunächst separat die Unter-, Mittel- und Oberteile, später das gefügte Komplettbauteil. Sie zieht Nuten für Kühlkanäle, setzt Bohrungen und ebnet die Oberfläche. Dafür braucht sie etwa eine Woche. „Hier Fehler zu machen, ist extrem teuer“, betont Billmeyer und weiß die Zuverlässigkeit der Maschine und seiner Kollegen zu schätzen.
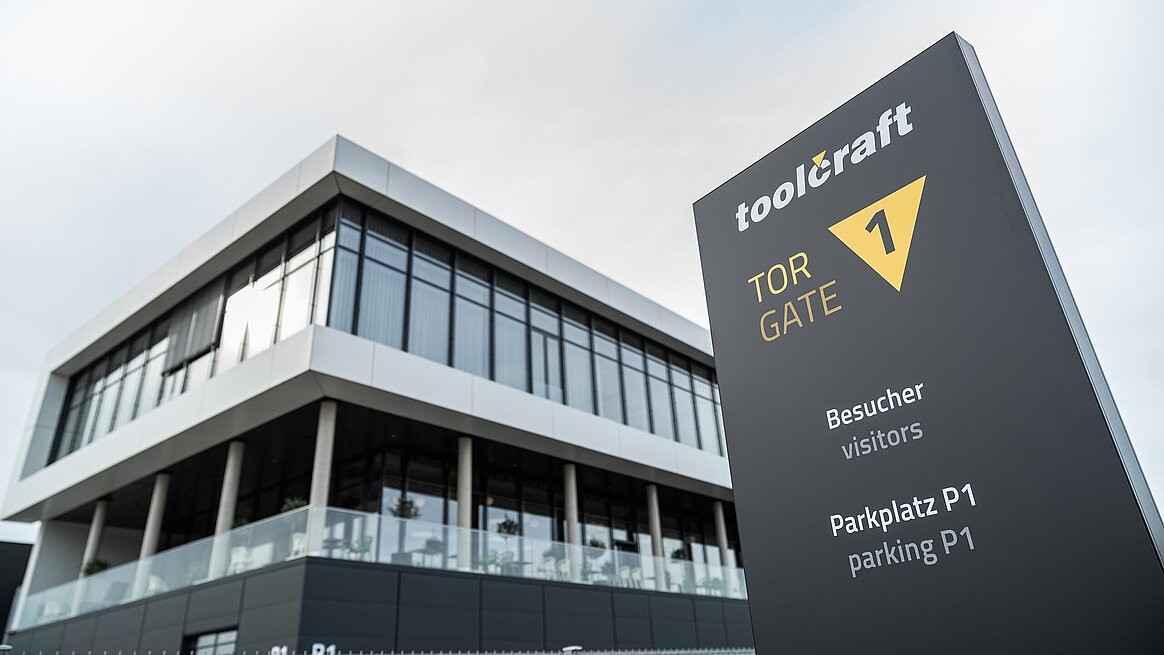
Millturn-Konzept spart Zeit
Deutlich kleiner geht es auf der C 42 U MT zu. Die Fräs-Drehmaschine steht einige Hallen weiter vorn, näher an der additiven Fertigung. Die Werkstücke, die hier unter die Spindel kommen, landen zu 70 Prozent in Flugzeugtriebwerken. Auch hier hilft das Maschinenkonzept toolcraft, sich selbst zu verbessern. „Wir haben das Bauteil schon davor gefertigt, mussten die Arbeitsprozesse aber splitten und waren überhaupt nicht zufrieden“, schildert Billmeyer. Zu viel Nacharbeit, zu wenig Perfektion. „Mit der C 42 U MT können wir die Frage vergessen, wann wir das Bauteil auf welche Maschine spannen müssen. Wir fräsen und drehen einfach dann, wenn es Sinn macht.“ Dank Messtaster, Lastüberwachung und integriertem Laser kann er die Fräs-Drehmaschine der Hermle High-Performance-Line bedenkenlos 16 Stunden am Stück arbeiten lassen. Das Ergebnis: Ein deutlicher Zeitgewinn bei besserer Qualität. „Dass wir dieses Niveau in der Genauigkeit und Maßhaltigkeit erreicht haben, hat selbst den Kunden überrascht“, erinnert sich Billmeyer.