Die Extrameile gehen
Höchste Präzision in der Werkzeug- und Spindeltechnologie – Werkzeugaufnahmen der Goldring-Serie sind hierfür ein gutes Beispiel. Die Helmut Diebold GmbH & Co. fertigt Highend-Zubehör für die CNC-Bearbeitung. Dabei nutzt das Unternehmen automatisierte Prozesse, zum Beispiel die Kombination aus 5-Achs-Bearbeitungszentrum C 42 U mit dem Robotersystem RS 2 von HERMLE.
Alles genauer machen, als es die Norm vorschreibt – so lässt sich das Motto von Hermann Diebold auf den Punkt bringen. „Rechnet sich das?“ überlegt der Geschäftsführer. Und beantwortet die Frage gleich selbst: „Nein. Wir bekommen dadurch nicht mehr Geld, aber die Kunden schätzen die Qualität unserer Komponenten und kaufen genau deshalb bei uns. Und wenn ich diese Präzision nicht hätte, würde ich sie haben wollen.“
1952 gründeten Helmut und Ida Diebold im schwäbischen Jungingen die Helmut Diebold GmbH & Co. Das Ziel: präzise Anlagenkomponenten für den Bau von Textilmaschinen zu fertigen. Mit den Jahren entwickelte sich das Unternehmen vom Lohnfertiger zu einem weltweit anerkannten Hersteller von Präzisionswerkzeugen. Heute umfasst das Spektrum hochwertige Werkzeugaufnahmen unter dem Namen Goldring, innovative Schrumpfgeräte, präzise Messtechnik sowie fortschrittliche Spindeln.
Mit mehr als 70 Jahren Erfahrung und 120 spezialisierten Mitarbeitenden legt das Unternehmen besonderen Wert auf höchste Präzision und Prozesssicherheit. „Unsere Produkte müssen sich perfekt in das Gesamtsystem Maschine-Spindel-Werkzeug einfügen“, erklärt Geschäftsführer Hermann Diebold, der die Geschicke des Betriebs in zweiter Generation lenkt. „Nur so lassen sich Drehzahlen im hohen fünfstelligen Bereich sicher fahren.“ Mit einem umfassenden Serviceangebot, einschließlich Kalibrierung und Reparatur, unterstützt Diebold seine Kunden dabei, maximale Produktivität und Effizienz zu erzielen.
Frische Impulse
Das Unternehmen erreichte in den vergangenen Jahrzehnten immer wieder technologische Meilensteine, etwa bei der Schrumpftechnologie. Diebold eroberte damit als Pionier frühzeitig den Markt, denn das Verfahren ermöglicht eine extrem steife und sichere Werkzeugspannung. Was früher mit einem Schweißbrenner umständlich erhitzt wurde, erfolgt heute vollautomatisch. Die neueste Generation der Schrumpfgeräte misst eigenständig Temperaturen, verhindert Überhitzung und kühlt selbstständig ab – mit einem einzigen Knopfdruck. „Unser ‚OneTouch‘ erleichtert dem Bediener die Arbeit und macht die Prozesse sicherer“, betont Hermann Diebold.
Automatisierung ist für ihn kein Selbstzweck, sondern ein essenzieller Hebel zur Produktivitätssteigerung. „Wir haben früh erkannt, dass wir Maschinen nicht nur effizienter, sondern auch smarter nutzen müssen“, blickt er zurück. Eine Maschine ohne Automation habe viel zu lange Stillstandszeiten. Dank moderner Bearbeitungszentren, wie der C 42 U mit angeschlossenem RS 2 von HERMLE, kann das Unternehmen hochpräzise Bauteile in personenlosen Schichten fertigen. „Unsere erste C 42 U kauften wir mit dem Wissen, dass sich der Automatisierungsgrad mit einem weiteren Bearbeitungszentrum nochmal spürbar steigern wird. Deswegen kommt in Kürze die zweite Maschine dazu“, verrät Hermann Diebold.
Läuft und läuft und läuft ...
Die C 42 U fräst sich mit voller Power durch komplexe Werkstücke – hochdynamisch und exakt. Das Robotersystem RS 2 steigert die Flexibilität erheblich, indem es Bauteile autonom und im Dauerbetrieb wechselt. Maschine und Roboter sprechen die gleiche Sprache, sorgen für einen reibungslosen Workflow und vermeiden Stillstand – selbst nachts oder am Wochenende. Das Zusatzmagazin ZM 192 hält genug Werkzeuge für längere Einsätze parat. Das Ergebnis: deutlich kürzere Durchlaufzeiten, geringere Kosten und maximale Prozesssicherheit – ohne Kompromisse bei Qualität oder Präzision. CNC-Fräser Marcel Heck sagt: „Während die Maschine arbeitet, kann ich mich um andere Aufgaben kümmern.“ Dabei lobt er auch die eingesetzte Software von Heidenhain: „Dank der dynamischen Vorschau und smarten Funktionen habe ich immer volle Kontrolle.“
Ein entscheidender Vorteil der Automatisierung liegt in der konstant hohen Qualität – von Losgröße 1 bis 100. „Viele unserer Werkstücke sind so präzise, dass wir jedes einzelne sofort vermessen, während die Maschine das nächste fertigt.“ Weniger kritische Bauteile zerspant der Betrieb in der Nacht und am Wochenende. „Das Limit sind nur die Palettenplätze“, weiß Hermann Diebold. Denn die meisten Teile laufen 20 bis maximal 40 Minuten auf der Maschine. Ganz besonders stolz ist er in diesem Zusammenhang auf seine Beschäftigten: „Es kommt oft vor, dass unsere Mitarbeitenden am Samstag kurz im Betrieb vorbeikommen, um die Maschine mit Nachschub zu versorgen. Viele von ihnen haben ihre Lehre bei uns gemacht, sind hochmotiviert und wollen etwas erreichen.“
Daten sind das Gold der Zukunft
Diebold setzt bei den eigenen Produkten nicht nur auf mechanische Präzision, sondern auch auf digitale Lösungen. Besonders spannend: eine neue Partnerschaft mit einem Start-up der Universität Hannover, das Sensorik für die Maschinendatenerfassung entwickelt. „Mit diesen Magnet-Sensoren lassen sich Maschinenzustände in Echtzeit überwachen – selbst bei älteren Anlagen ohne moderne Steuerung“, erläutert Hermann Diebold. Eine künstliche Intelligenz bewertet die erfassten Daten und ermöglicht dadurch Predictive Maintenance. Das Ziel: die Wirtschaftlichkeit verbessern. „Anfangs hielt ich es für einen Scherz, dass allein durch die Visualisierung der Maschinenzustände die Produktivität um 15 Prozent steigen soll. Heute weiß ich: Es stimmt.“ Damit lassen sich auch einzelne Aufträge tracken und Plan- sowie Ist-Zeiten vergleichen. „Das ist etwas, das wir heute unbedingt brauchen. Der Kostendruck ist immens, wir müssen daran arbeiten, alle Potenziale bestmöglich zu nutzen.“
Und natürlich setzt der Unternehmer auch bei der HERMLE-Maschine auf digitale Unterstützung. Die HIMS (HERMLE Information-Monitoring-Software) zeigt als zentrales Überwachungstool eine kompakte Übersicht der C 42 U mit einem Live-Status. Alle Daten, auch solche aus der Vergangenheit, lassen sich detailliert auswerten und exportieren. Im Fall eines Fehlers oder Ereignisses informiert das System via HIMS-Server den Anwender mit einer E-Mail. „Damit wissen wir ganz sicher, ob und wann wir eingreifen müssen“, betont Hermann Diebold.
Klimaneutrale Fertigung
Neben Akkuratesse und Innovation treibt den Unternehmer auch Nachhaltigkeit um. Diebold produziert nahezu klimaneutral: „Wir setzen auf einen Energiemix, der ohne fossile Brennstoffe auskommt“, betont der Geschäftsführer. Die Fertigungshallen sind gut isoliert, Wärme bezieht der Werkzeugspezialist von einem Nachbarn, der aus Holz und Hackschnitzeln Bioenergie gewinnt. Die Abwärme der Kompressoren versorgt die Fußbodenheizung. Zur Klimatisierung der Hallen nutzt Diebold ebenfalls mehrere Systeme: Bis etwa 12 Grad Celsius Außentemperatur kühlt Frischluft das Zirkulationswasser, darüber verwendet der Betrieb das Wasser des benachbarten Bachs als Kühlmedium. Nur in den heißen Sommermonaten übernimmt ein zusätzliches Lüftungsklimagerät mit sehr hohem Wärmerückgewinnungsgrad die Kühlung.
Die konstante Raumtemperatur sorgt dafür, dass Werkstücke, Werkzeuge und Maschinen stets unter optimalen Bedingungen arbeiten und höchste Genauigkeit gewährleistet bleibt. „Je anspruchsvoller unsere Kunden sind, umso lieber ist uns das. Denn durch unsere Qualität können wir uns vom Wettbewerb abheben.“ Und noch etwas sei entscheidend: „Gute Produkte haben die längste Lebensdauer – das ist wahre Nachhaltigkeit. Auch deswegen setzen wir auf Maschinen von HERMLE.“
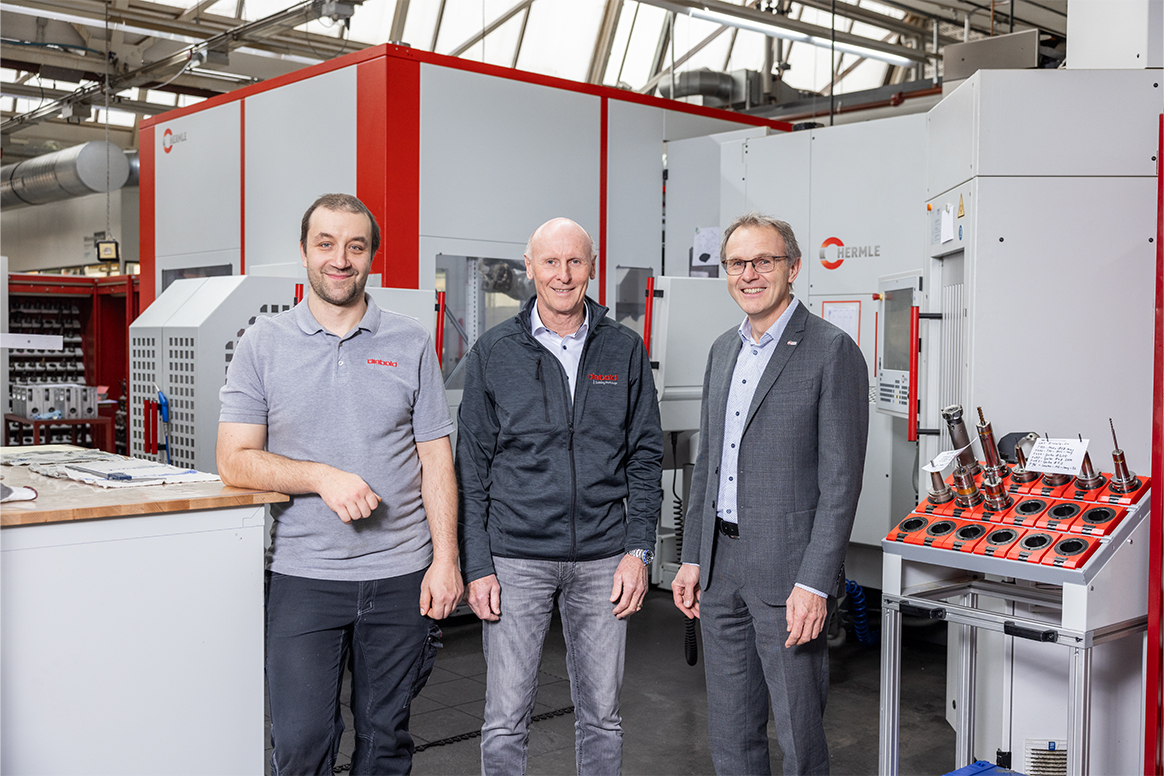