Robot system on a new level – GEN2 version of the robot system RS 2
HERMLE AG has been investing in the automation of its machining centres for more than 25 years. Simple pallet changers were soon followed by compact handling systems, and robots have played a key role from the start. In the meantime, HERMLE has made a name for itself through its automation solutions and successfully added a second string to its bow. The customer purchases both main components from a single manufacturer and has just one point of contact in the event of service issues. “Everything from a single source” is more than just a slogan at HERMLE; it is a real and valuable advantage that is valued by customers just as much as the HERMLE service benchmark.
With the GEN2 version of the robot system RS 2, HERMLE AG is again taking automation to a new level. Nearly all areas of the previous RS 2 system have been enhanced and optimised to better meet customer needs.
The system is platform based and can be customised through various modular configurations. This also makes it possible to adapt the system to one, two or even three identical or different HERMLE machining centres. The safety enclosure is extensively glazed to provide a clear view of the interior and, with up to three double access doors, ensures optimum operator protection, especially during manual work on the machine. Various setup station variants enable the convenient loading of workpieces into the system. Six rack modules ensure extensive and convenient workpiece storage. The system is designed for the storage of pallets, workpiece carriers or dies and, of course, storage pockets for an array of grippers. Positioned in the centre of the system, the six-arm robot is designed to efficiently load all working areas of the machines, while handling transport weights of up to 210 kg. Like all HERMLE machines, the system is transported in one piece without disassembly, ensuring fast and smooth installation and commissioning.
The robot system is therefore composed of several main components, which are outlined and examined in detail below.
- Base platform in four expansion stages with fully glazed safety enclosure
- Six-axis robot with a load capacity of 210 kg
- Two setup station systems with workpiece height measurement and width control
- Six individual rack modules with an intelligent storage strategy
- Up to three transfer stations for workpiece handling
- Various gripper, clamping, pallet and die systems
- Control software for perfect operation and machining strategy
-
The robot system RS 2 GEN2 with two adapted C 32 five-axis machining centres -
Laser monitoring system of the robot system RS 2 GEN2 -
Individual rack modules with an intelligent storage strategy
of the robot system RS 2 GEN2 -
Footprint for the first expansion stage of the robot system RS 2 GEN2
with two adapted C 32 five-axis machining centres -
Five of the six rack modules for the robot system RS 2 GEN2
Base platform in four expansion stages with fully glazed safety enclosure
The base platform has a footprint of just 13 m2, with main dimensions of 4.25 x 3.00 x 3.25 m (L x W x H). Expansion stage 1 has a footprint of just 16 m2, with main dimensions of 5.50 x 3.00 x 3.25 m (L x W x H). It features a welded construction, which is manufactured at HERMLE’s sheet metal production facility, and supports the six-arm robot, rack systems and safety enclosure. It is extensively glazed and gives the operator a good view of the system interior.
Six-axis robot with a load capacity of 210 kg
The six-axis robot is located at the centre of the system and is permanently mounted on the platform. Due to its optimised arrangement, it can reach up to three working areas, up to six rack modules, the setup station and the two storage positions, with a transport weight of up to 210 kg.
Two setup station systems with workpiece height measurement and width control
A manual or optional rotating setup station can be adapted to the system. It boasts extensive glazing and two rotating doors which, when opened to load the setup station, also close off access to the system. A special feature concealed behind the setup station is the laser monitoring system. It measures the workpiece height and checks the maximum width of the pallets/fork systems before the robot places the pallet or carrier module with the die from the setup station into the rack modules. The control software quickly and easily identifies available free capacity in the rack module, thus placing the pallet/fork system into the randomly organised storage system in a space-optimised way. This ensures effective rack filling.
Six individual rack modules with an intelligent storage strategy
The six basic rack modules offer a wide range of storage options and variants. Thanks to the continuously adapting levels of storage in the new width-flexible and height-optimised racks, manual rack adjustments are significantly minimised. This means that there is no need for rigid rack organisation as was previously the case. This task is now assumed by the control software, which places the pallets/fork systems randomly in the rack modules, while optimising the footprint perfectly. The number of rack modules that can be used basically depends on how many machines are adapted to the robot system.
Up to three transfer stations for workpiece handling
To switch from pallet handling to parts handling, one, two or three transfer stations for storing the pallets/carrier modules are available in the working area of the robot system, depending on the number of adapted machines. After a gripper changeover, it is possible to switch between handling pallets with workpieces or individual workpieces. For example, with a two-machine solution, workpieces can be produced on pallet carriers in one machine and as individual workpieces in the other. High level of flexibility without any restrictions.
Various gripper, clamping, pallet and die systems
An array of grippers is one of the most crucial components in a robot system. HERMLE uses standard or hybrid grippers, either as single or double grippers, in its robot systems for parts handling. The standard single and double grippers can be adjusted manually from 8 to 319 mm. The transport weight per gripper is 20 kg. The hybrid single and double grippers are adjusted automatically from 10 to 240 mm. All the grippers can be adapted with an array of gripper fingers. The transport weight of the hybrid gripper is 25 kg, while the weight of a double hybrid gripper is 2 x 25 kg.
An NSR gripper is adapted to the robot for handling pallets and die carriers. It can transport pallets weighing up to 210 kg and die carriers up to 600 x 600 mm in size and 180 kg in weight. In addition to standard dies with a standardised grid for identical components, HERMLE universal dies can also be used, offering individual adjustment for a wide range of part families.
To offer fully automated and effective machining and parts handling, the clamping jaws of the vices can also be changed fully automatically in the RS 2 GEN2. This enables an even greater number of workpieces and is the ideal addition in the area of six-sided machining.
Control software for perfect operation and machining strategy
The control software is the heart and soul of the system. It manages, checks and coordinates the workflow within the system. It communicates with the operator and displays the system status. Intelligent alternative strategies in the order sequence (e.g. broken tools, non-processable orders or switching to an alternative order where everything is available). Ideal ToDo preview for operator activities with a multi-day forecast. Flexible planning options across several machines.
The advantages again at a glance
- Compact, highly modular robot system in four expansion stages
- Space-optimised design of just 13 m2 or 16 m2
- Cutting-edge design and can be combined with up to three HERMLE machines
- Up to seven machine models from both HERMLE series can be adapted
- Six different individually configurable rack modules for maximum flexibility
- Various grippers, pallets, dies, carrier modules and clamping jaws
- Transport weight of up to 210 kg
- Operator-friendly control software for system operation, order and process management as well as sequence control
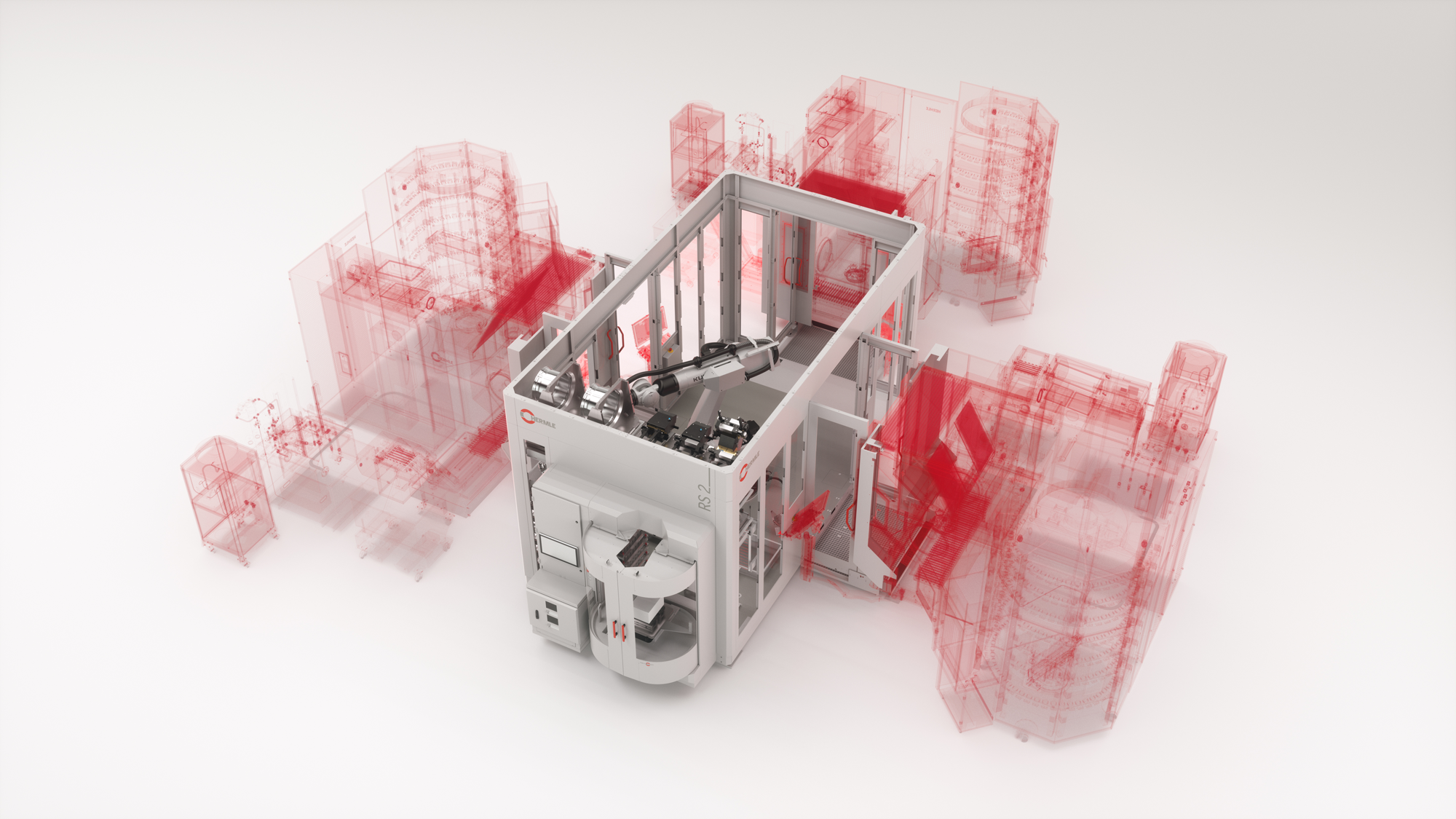
Contact details for journalists/editors:
Maschinenfabrik Berthold HERMLE AG / Marketing Department / Email: marketing@hermle.de / Phone +49 (0)7426 95-0
78559Gosheim