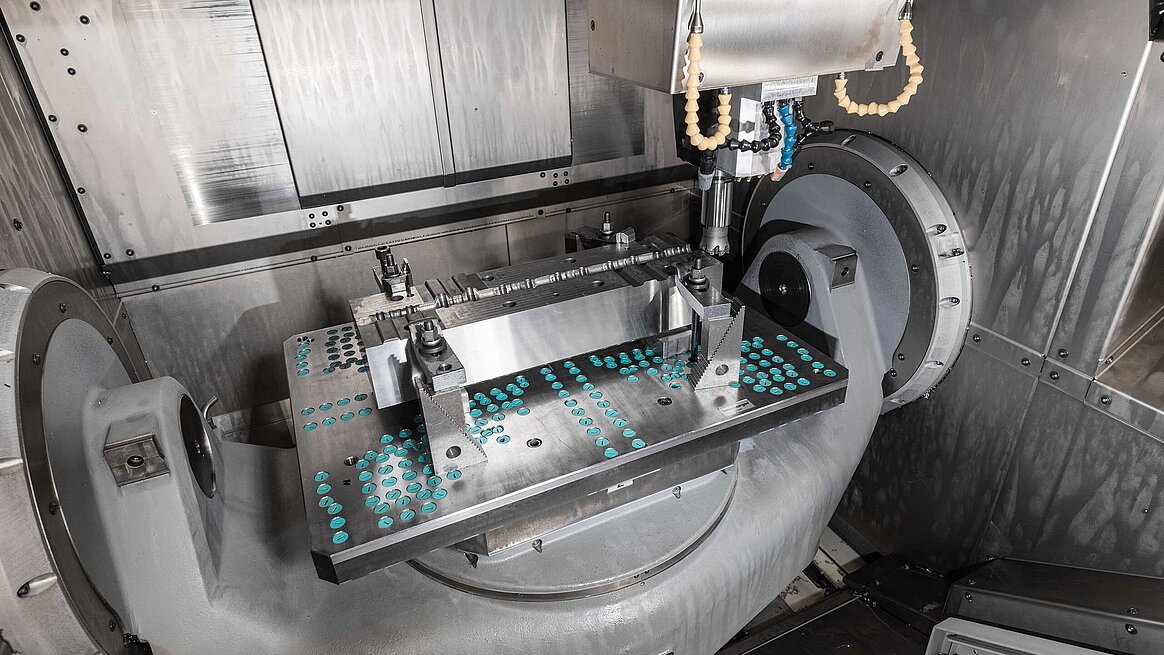
PERFORMANCE, PRECISION AND 5-AXIS KNOW-HOW
After an intensive analysis of the current and future range of parts and requirements, the decision was taken in favour of a 5-axis CNC high-performance machining centre C 42 UP with a PW 850 pallet changer. This machine offers all the prerequisites for universal, flexible 5-axis simultaneous machining in one or just a few setups – from roughing and finishing to hard milling and finishing after surface treatment. In order to be able to carry out these machining operations properly and in a manner that is gentle on the machine and tools in two-shift operation, plus an unmanned third shift, those responsible ordered additional controller functions and machining setups. They allow μ-Tec to adapt the machine dynamics according to accuracy, surface quality and machining speed requirements as well as the machine behaviour to the respective machining task. The combination of the machine concept, featuring three axes in the tool (X, Y, Z) and two axes in the workpiece (C, A), with the high degree of accuracy and reliability guarantees high-precision and reproducible machining quality. And this ensures the service provider the highest level of performance for its discerning customers.
The Hermle machining centre at μ-Tec GmbH in Chemnitz, consisting of a 5-axis machining centre C 42 UP and a PW 850 pallet changer with front sided setup station PW 850 top the large working range of the C 42 UP with traverse paths of X-Y-Z = 800-800-550 mm and the swivelling rotary table measuring 800 x 630 mm in diameter for clamping interchangeable pallets; in this case equipped with a universal grid plate to accommodate various workpiece clamping devices bottom from left to right, Heribert Quast, Managing Partner, Matthias Taubert, Production Manager, and Nico Richter, machine operator of the 5-axis CNC high-performance machining centre C 42 UP, all from μ-Tec GmbH in Chemnitz