Precision for the view on the antibodies
C 32 U HS flex | EUROIMMUN | Medical technology
The components are made on 5-axis machining centres from Hermle. In addition to the high precision and reliability of the machines EUROIMMUN is also convinced by the HS flex automation solution: It offers maximum flexibility for the machining operators with regard to the parts range and production scheduling and at the same time minimises non-productive times.
Genes are the smallest functional units in DNA and together with environmental influences determine the generation of specific characteristics. They are detected and analysed with the aid of molecular diagnostics and thus furnish proof of genetic disorders or predict the effect of specific drugs. In addition, state-of-the-art analysis methods detect smallest amounts of DNA of bacteria or virus and consequently are a vital element of molecular infection diagnostics. It is based on methods requiring absolute precision and comprehensive know-how. EUROIMMUN AG has both. Since 1987 the Lübeck-based company produces reagents for laboratory diagnostics of autoimmune and infectious diseases, allergies and genetic analyses. The development and production of fully automated analysis systems started in 1999, consisting of automatic incubators and microscopes with computer-based evaluation in IFT (immunofluorescence technology), or for the ELISA detection method (Enzyme-linked Immunosorbent Assay) also based on antibodies. EUROIUMMUN AG today, being a part of the US medicine and biotechnology company PerkinElmer since 2017, is doing business all over the globe. Branch offices are located in Groß Grönau near Lübeck, Dassow and Selmsdorf, Rennersdorf and Bernstadt, and Pegnitz. In addition there are 14 other local branches worldwide. The laboratory expert has 3,000 employees across the world.
Unique combination
"Our unique feature is that we do not develop and offer diagnostics only but also efficient automation solutions for laboratories," sais Martin Rateike, Division Manager Design Engineering, Production and Assembly at EUROIMMUN AG. The graduated biomedical engineer has been working for the company for over 25 years and takes part in the design and engineering of the devices right from the start. In 2012 he ordered the first machining centre from Maschinenfabrik Berthold Hermle AG – a B 300 U. "We had invested before in the milling machine from another manufacturer and were disappointed particularly with regard to reliability", Rateike remembers. "Machine failures can never be excluded but it must be possible to eliminate them easily and quickly." Hermle clearly scores points here with its reliable service," the Division Manager sais. Quality and design are also absolutely consistent for the responsible manager. "If an accidental collision is caused, it is not necessary to replace the entire spindle thanks to the compression sleeves," Alexander Schmalz, Head of the Machining and Production Department at EUROIMMUN sais.
The laboratory diagnostics specialist is currently building between 300 and 500 serial instruments a year. In addition there are various production facilities for the production of various in-house diagnostic instruments. "The production figures are much variable – and we unable to do long-term planning," Martin Rateike explains. "Two years ago we were looking for milling centres with a connected automation system to increase our in-house production depth and still remain flexible with regard to production." Rateike is sceptical about bought-in systems not produced by a single manufacturer – he fears long downtimes in the event of faults and unclear responsibilities.
A convincing prototype
When visiting Hermle in Gosheim in February 2017, the decision-makers from EUROIMMUN were able to cast a glance on the HS flex system prototype. "The concept seemed promising to us. Consequently we had the courage – in relying on Hermle Service – to take the risk and ordered a C 32 U with the new automation solution," Rateike remembers.
With the C 32 U it is possible to machine workpieces up to the diameter of 650 millimetres and height of 450 millimetres. The drive concept of the swivelling rotary table with worm drive enables precise positioning of the workpieces to be machined. This is thanks to drive engineering directly acting on the gearwheel at the machining table housing and thus reducing shaft torsion to a minimum. "it was out of question that Hermle is able to satisfy the demands on precision. The desired flexibility was implemented by the HS flex automation among other things due to the option of individually configuring the rack storage modules for mixed operation with different workpiece and pallet dimensions," Thomas Mielke from HPV Hermle Vertriebs GmbH explains. Martin Rateike agrees: "The first machining centre with HS flex showed us that the handling system is the perfect solution for our requirement – we are able to manufacture different parts in variable numbers quickly and precisely. This is also one of the reasons why we ordered three further milling centres from Hermle with the HS flex automation system in two years." In addition to two C 32 Us one C 22 U and the C 400 U, each with two pallet storage modules, are currently available in the production building in Dassow built in 2017. "With the second C 32 U we produced in house all parts formerly subcontracted which fully utilised both machines for months at first," Schmalz adds
Praise for an intuitive operation concept
Commissioning ran smoothly for all four machines. The division manager considers the intuitive operation of HS flex as particularly outstanding. His employees were able to operate the system without any problems after familiarisation without separate training. Core element is a touch pad with the integrated HACS (Hermle Automation Control System) software. It assists in intelligent job processing and displays all relevant data – from the system overview and the job schedules via pallets, tasks and tool tables up to the sequence plan.
Usually one employee is responsible for two machines, and at peak times even three machines at the same time. Combined with unmanned shifts this offers precious leeway in production scheduling for EUROIMMUN. The milling centres are programmed directly via the Heidenhain TNC 640 control unit. "It requires appropriate know-how, makes working with the machines interesting and thus motivates the operators. In addition it shortens the manufacturing expenditure for us as we can program individual changes directly on site instead of using the route via a CAD/CAM program," Alexander Schmalz explains. Redundant parts can be called from the rack storage directly and further optimised in the process.
Manufactured are, amongst other things, components for the fully automatic microscope with computer-aided IFT evaluation and automatic pattern matching or tracks for the ELISA EUROLabWorkstation, in which the pallets with the samples and reagents are stored. "The challenge is the large number of variants: We produce geometrically simple as well as highly complex parts with side lengths from five to 580 millimetres. Usually we mill-cut from solid material – about 75 percent of aluminium," Schmalz explains. High precision is what counts here. "Our fully automatic microscope has to position with the accuracy to the micrometre. To achieve this with a high repeat accuracy, we require an appropriate dimensional accuracy for each individual component. The Hermle machines produce so precise that the overall structure satisfies this accuracy later on," Rateike explains.
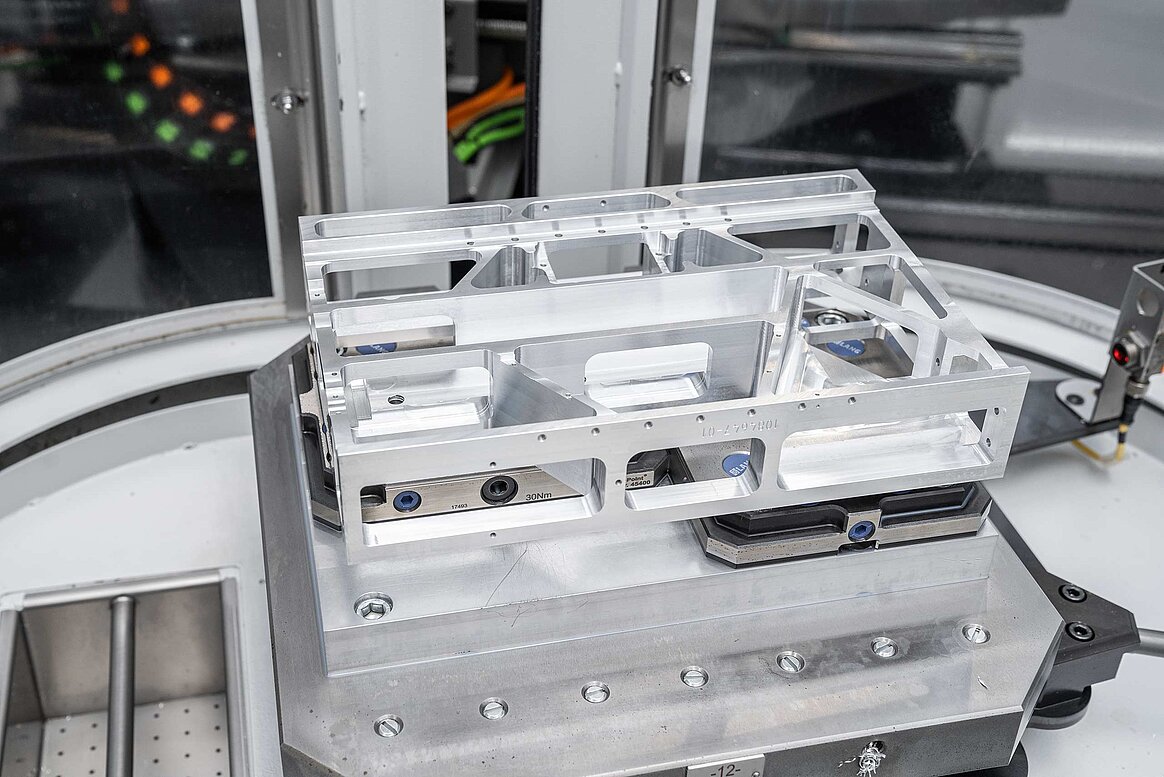
Saving setup time
Another aspect, in addition to flexibility and precision, was decisive for EUROIMMUN to increasingly invest in Hermle machines: This was optimising times. The workpieces are machined between 20 minutes and six hours. "Thanks to the HS flex system we are able to set up efficiently and load the pallet storages in a half shift without having to interrupt the machining process," Schmalz adds.
"Thanks to the Hermle machines we increased our in-house production depth – we produce milling parts by 98 percent in our workshops now thus saving time and money," Rateike concludes. The automation system makes unmanned shifts possible and helps to balance peak times in the best possible way. Throughout 2019 the four milling centres with HS flex automation are already utilised by about 90 percent and offer EUROIMMUN the security to be able to manufacture independently and flexibly without having to give away technological know-how.