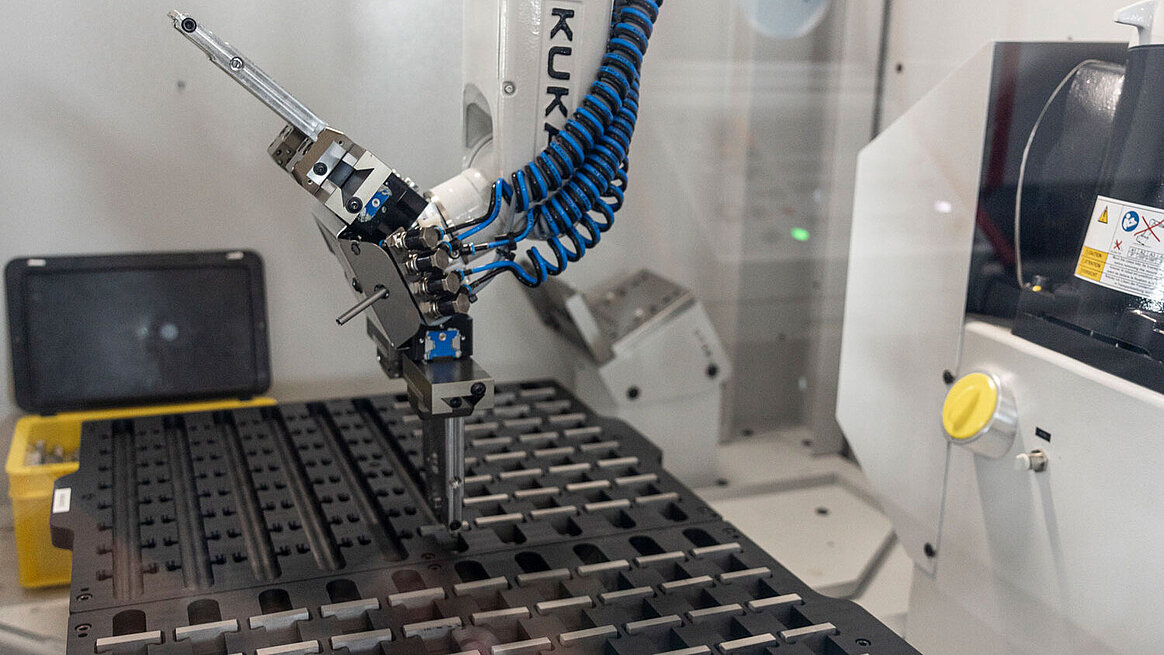
First robot in operation
Four additional HERMLE C 12 U RS 05 machining centres have been installed in the milling shop since the beginning of 2023. hg medical previously automated all of its machines with the IH handling system. The four new systems are the first to be equipped with robots. They insert blanks into the chuck, clamp the semi-finished part and remove the finished milled implant. At the other systems, a workpiece changer supplies the milling centres with pre-loaded material, thus enabling unmanned automatic operation. “We have lots of small-scale series. The investment plan for the RS 05 systems was finalised following an order from a customer for significantly larger quantities of their products. We wanted to be faster and to reduce labour costs,” reports Lukats. How? By introducing robot-assisted milling centres to handle a work step that was up to now only possible manually.
“We previously milled the implants in one clamping setup. This left us with two support rods that had to be removed and their remnants ground down manually,” explains Lukats. To enable the C 12 U to mill away the small protrusion, a second clamping device and a gripper are required to move the component. The special feature: To work extremely precisely, the image is the negative of the bone plate. “After the initial milling process, the gripper takes hold of the semi-finished implant and places it within the negative die. Positional holes ensure precise placement, allowing the machine to process the surface with the same precision as in the initial clamping.” The plate is ready for surface treatment and quality inspection after 19 to 25 minutes.
Three times the benefit
“We have high expectations when it comes to robot automation: It should save time and effort while maintaining or even improving overall quality. And HERMLE achieved these goals,” explains Lukats. hg medical has eliminated the need for manual grinding, which always posed a risk of errors. Further, the company has also optimised the preparatory phase. Instead of pre-stamping the blanks and clamping them in vices, as required by other automation systems, the operator simply pushes a die with the titanium or stainless-steel plates into the robot cell.
When concluding, Lukats additionally highlights another distinct advantage of HERMLE robots: “Modern high-tech machines inspire people. The new technology is a motivational boost for our employees and helps fuel our growth.”