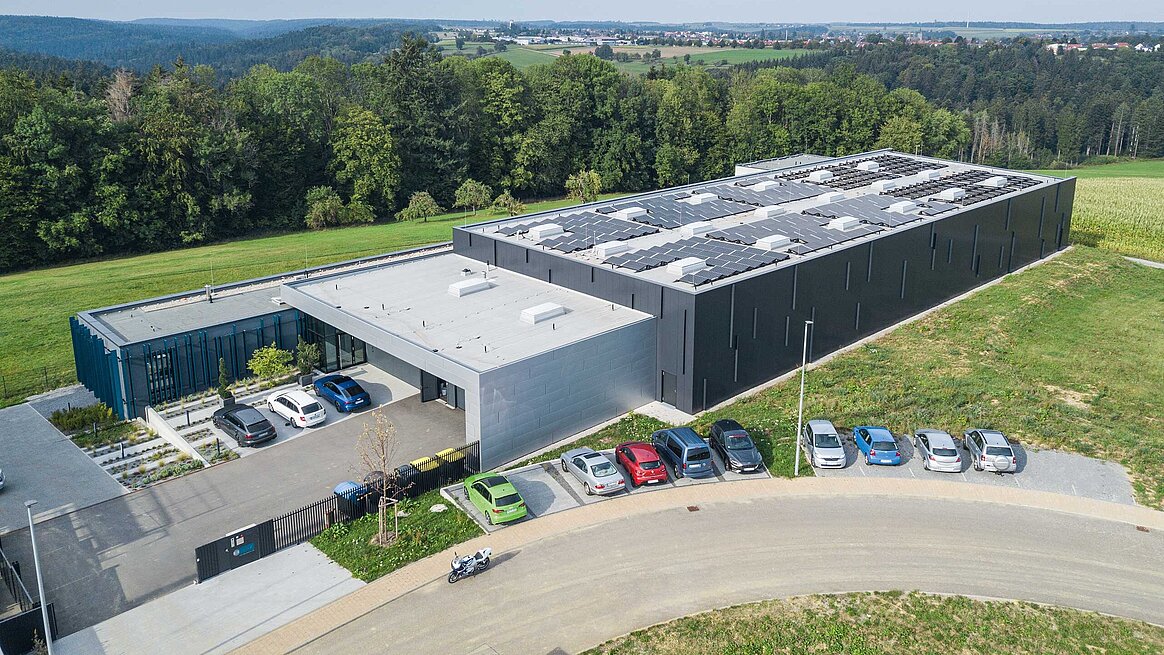
Automation times two
In 2018, production again reached the capacity limit and Schulz decided to invest in a C 42 U with HS flex automation. "At first we really had respect for the automation," Michael Schulz admits. But the fear of producing rejects and the feeling of uncertainty while the system was running unmanned proved to be completely unfounded.
"The automated system accomplishes as much as three of our stand-alone machines while relieving our employees of monotonous, repetitive tasks," Schulz says. As a result, the automated machining centre reached over 5,000 spindle hours within a year and was quickly running at over 100 percent utilisation. Convinced of the stability and benefits, the management team ordered a second C 42 U with flexible automation solution. "We now have a bit of leeway which we can use for maintenance work, for example," Schulz says. He also has Hermle do the maintenance work: "This makes perfect sense. After all, the Hermle technicians know the machines best and know what needs to be done."
Alfred and Michael Schulz are fully convinced of the stability and accuracy of all their Hermle machines. "We machine some of the components for weeks. Even after four weeks we need not make corrections. We are working in the tolerance range of five µ," Michael Schulz explains.